House of Sumaavi
Hand blockprinted Chanderi Silk Stole
Hand blockprinted Chanderi Silk Stole
SKU:APSTC00001
Specifications:
Specifications:
Size: 2.3 metres
Weight:
Color: Olive Green
Material: Chanderi Silk by Cotton
Frame:
Content:
Couldn't load pickup availability
This beautiful stole has been designed and hand blockprinted by artisans of Akola village in Rajasthan. Made in Chanderi Silk by cotton fabric, it is a perfect choice for pairing with salwar kameez or a shirt, dress and virtually anything in your wardrobe.
Care Instructions
Gentle wash with mild detergent
Note :
“Ours are genuine hand block printed products made by artisans of Rajasthan, India. Kindly be aware of machine printed products being sold online in name of hand blockprints.”
Craft Story
Craft Story
Sarees and stoles hold a significant place in India's cultural heritage, reflecting the country's rich and diverse history. The saree is a traditional garment draped around the body, while the stole is a long piece of fabric elegantly wrapped around the neck or shoulders. The versatility of these clothing items has made them a favorite among fashion enthusiasts worldwide, perfect for any occasion or event, be it formal or casual. The lightweight and breathable nature of cotton sarees and stoles make them a perfect choice for hot and humid summer days, offering comfort and style simultaneously. With a variety of fabrics, designs, and patterns to choose from, these traditional garments continue to evolve and inspire contemporary fashion trends, making them a timeless and iconic part of India's fashion heritage.
Sumaavi an Emerging Brand for Handmade Sarees & Stoles
Looking for something unique and handmade? Look no further than Sumaavi!
Our brand offers a wide range of sarees and stoles, all made with care and attention to detail by our talented artisans. From contemporary designs to traditional patterns, we have something to suit every taste. At Sumaavi, we are proud to support our community of makers and designers. Our products are crafted with love and tradition, making them special and unique. Our sarees and stoles are perfect for those looking to infuse their style with a touch of elegance and sophistication. With vibrant colors and unique designs, you can choose from the wide range of products available online, and you’ll surely find something that fits your aesthetic perfectly. Our website features a variety of options, from the newest trends to timeless classics, so you can always stay on top of the latest fashion. Whether you're looking for something to wear to a special event or just want to add a touch of elegance to your everyday wardrobe, we have you covered.
Explore the Exquisite collection of Handmade Sarees & Stoles from Sumaavi
At Sumaavi, we take pride in offering the finest and most luxurious collection of handmade sarees and stoles. Our exquisite collection includes hand blockprinted Chanderi silk saree and hand blockprinted Kota Doriya stole, both known for their intricate work and high-quality fabric.
Chanderi silk sarees and stoles are a perfect blend of silk and cotton yarn, originating from the Chanderi village in Madhya Pradesh. They have a rich history and are considered a classic addition to any wardrobe. On the other hand, Kota Doriya sarees and stoles are made from pure cotton and silk, originating from the Kota district in Rajasthan. These sarees and stoles are a symbol of elegance and grace, and their intricate designs are a testimony to the artisans' exceptional craftsmanship.
Our collection of Chanderi silk and Kota Doriya sarees and stoles are perfect for those who value quality, elegance, and luxury. They are renowned for their lightweight and airy nature, making them ideal for any occasion, from formal events to everyday wear. Choose from our wide range of designs, and you are sure to find the perfect saree or stole to complement your style.
Discover Handmade Sarees and Stoles Only at Sumaavi
Sumaavi is the perfect destination for those seeking high-quality handmade sarees and stoles. Our collection boasts exquisite blockprint items, crafted with intricate work and premium fabrics. At Sumaavi, we pride ourselves on supporting our community of artisans and designers. By offering unique and handmade products, we provide our customers with a touch of luxury and sophistication. When you shop at Sumaavi, you'll discover a world of beauty and craftsmanship. Our collection features a wide range of designs, from contemporary to traditional, ensuring that there's something for everyone. So why wait? Start exploring our collection of handmade sarees and stoles today and experience the beauty of Indian craftsmanship.
Shipping & Returns
Shipping & Returns
Shipping: Free shipping across India. International shipping on request.
Returns: This item is not eligible for return or replacement. There is a possibility of minor color variations from the image shown on the website, as it depends on the screen brightness of the device and the photography. This is a handcrafted item; cherish the little imperfections in the make of the product; these imperfections make them unique. In the unlikely event that a damaged, defective, or different item is delivered to you, the return will be considered within five days of delivery. Please write to us on contact@sumaavi.in for return request in such cases.
Disclaimer
Disclaimer
All rendered images are for illustrative purpose only.
Every product at Sumaavi is a masterpiece made by artisans and carries with it the tales of tradition. As a result, there can be some differences between the actual product and the photograph. You may expect minor differences and imperfections that make your product unique and exceptional because these variances are natural in the manufacturing of handmade goods. These little differences make your product truly special and unique.
Share
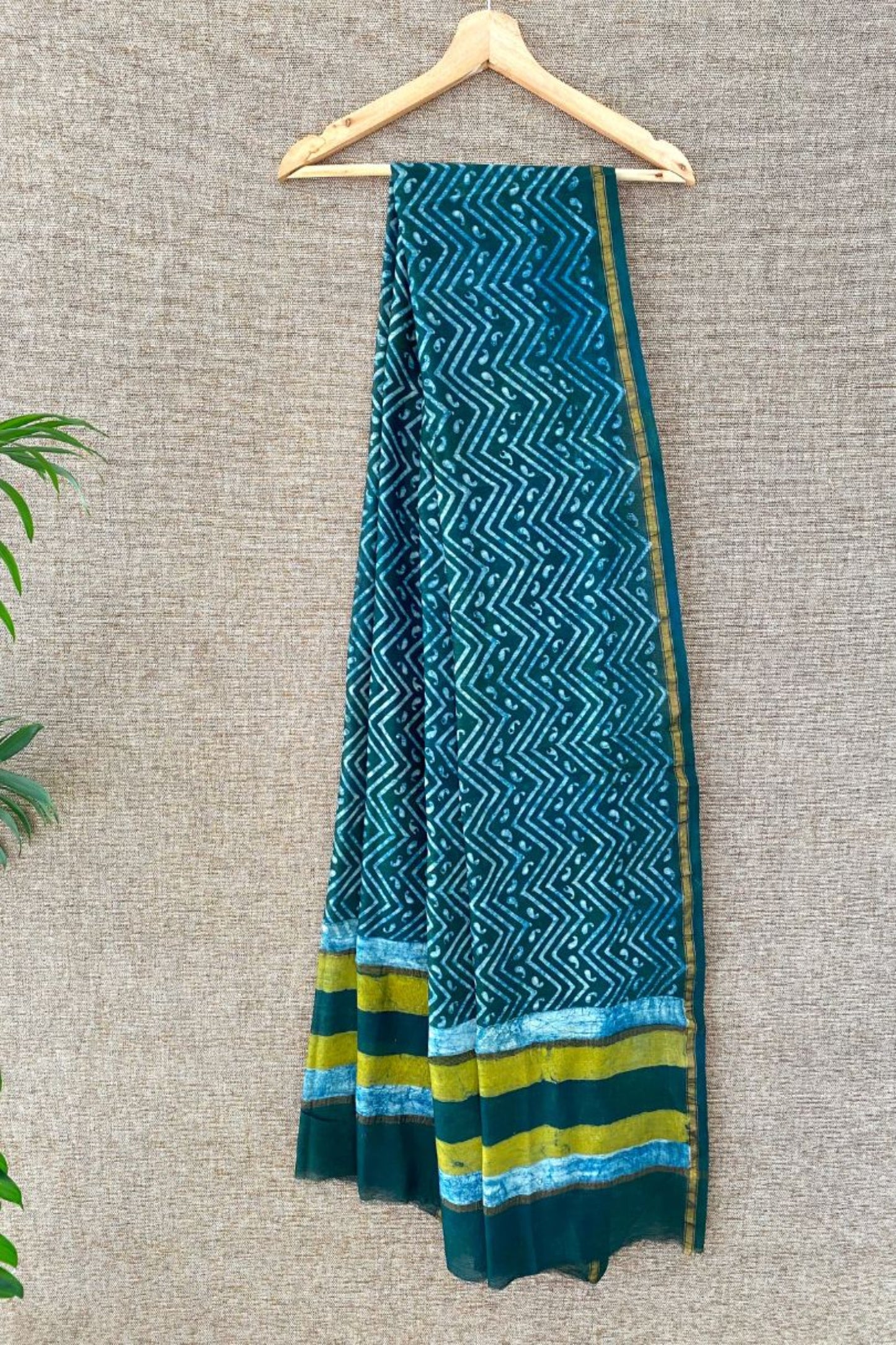
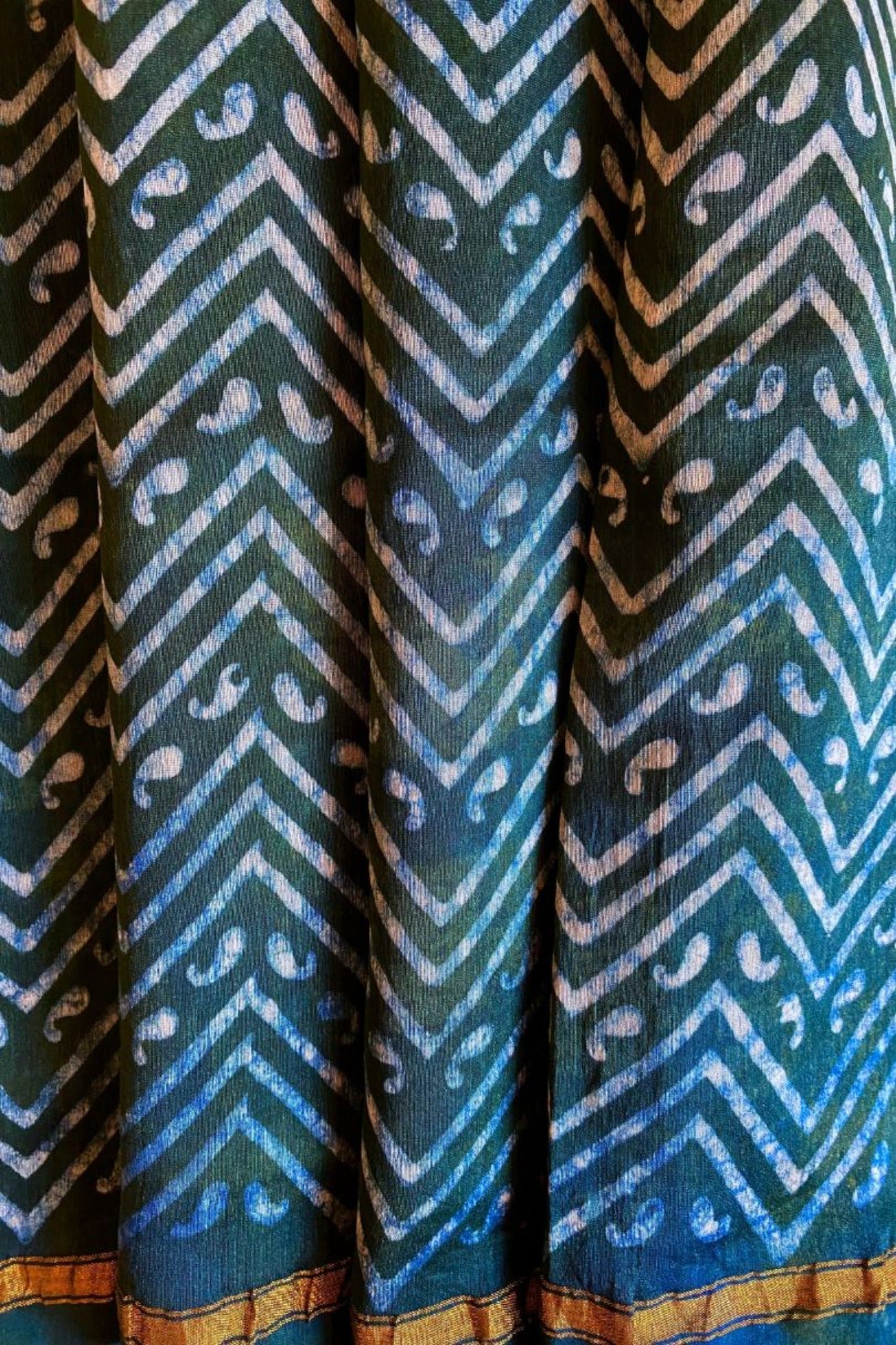